The Low Pressure Casting Process: A Comprehensive Guide
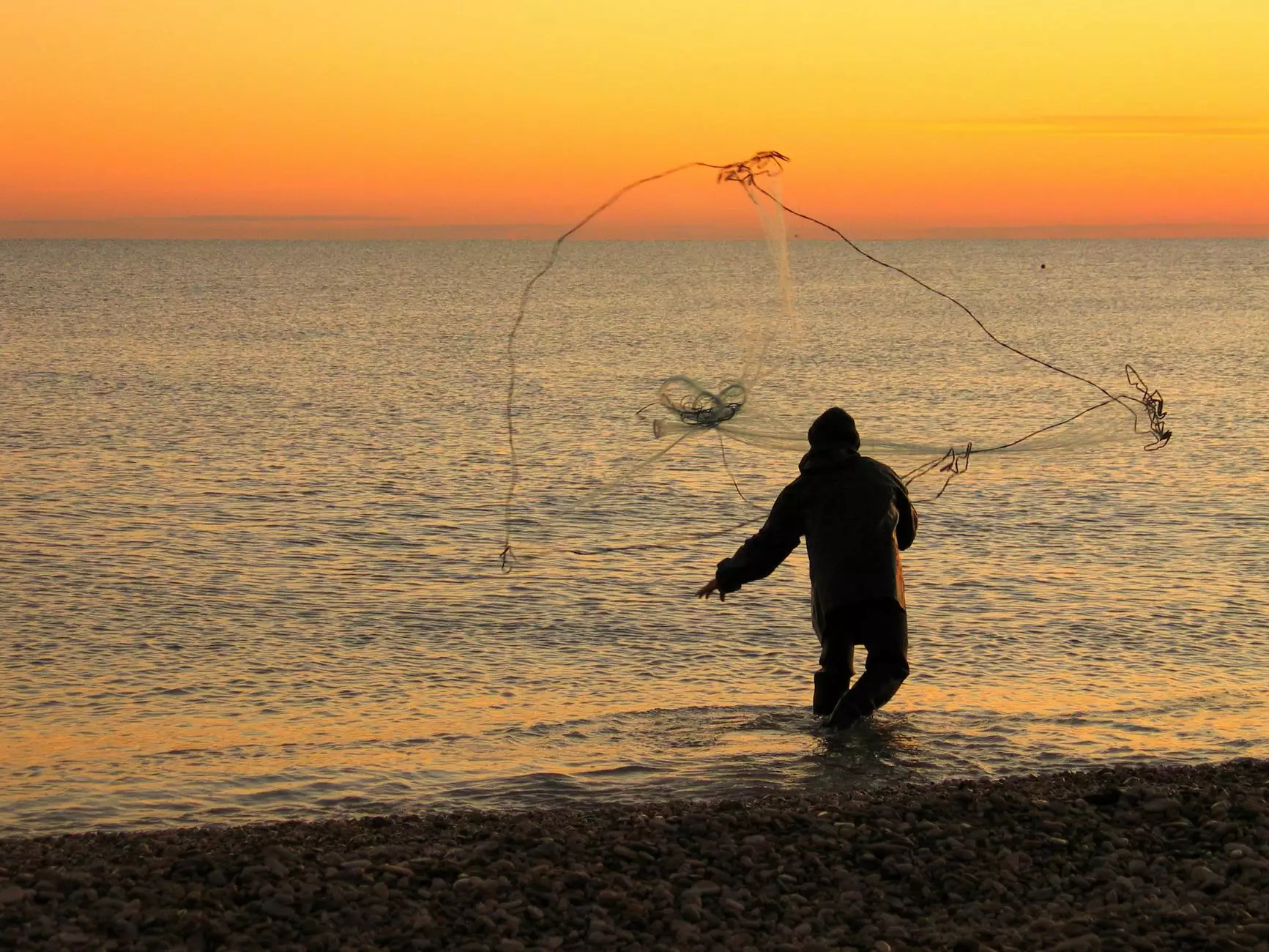
In the realm of manufacturing and product design, the low pressure casting process has emerged as a dominant technique that streamlines production while enhancing quality. This method has become increasingly significant in various industries, particularly in the creation of intricate designs with superior surface finish. In this article, we will delve deep into the low pressure casting process, its benefits, applications, and how it shapes modern manufacturing.
What is Low Pressure Casting?
The low pressure casting process is a metal casting technique that involves the use of low pressure to fill a mold with molten metal. Unlike traditional gravity casting methods, where metal flows into the mold by the force of gravity, low pressure casting uses air pressure to push the molten metal into the mold. This innovative approach allows for better control of the metal flow, reducing the likelihood of defects and enhancing overall product quality.
The Process Explained
To understand the low pressure casting process, it's vital to break down the steps involved:
- Mold Preparation: High-quality molds are crafted, typically from durable materials like aluminum or steel. These molds are designed to create a specific object with high precision.
- Metal Melting: The selected metal, often aluminum or zinc alloys, is melted in a furnace. The molten metal must reach a certain temperature to ensure optimal flow properties.
- Low Pressure Injection: Once the metal reaches the desired temperature, it is injected into the mold under low pressure, usually ranging from 0.1 to 0.3 bars. This process forces the metal to fill the mold uniformly.
- Cooling and Solidification: After the mold is filled, the molten metal is allowed to cool and solidify. The speed of cooling can be controlled, which impacts the final properties of the casted object.
- Mold Removal: Once solidified, the molds are opened to extract the finished product, which often requires minimal post-processing due to the high-quality finish achieved during the casting.
Benefits of Low Pressure Casting
The low pressure casting process offers numerous advantages that make it a preferred choice for manufacturers and product designers alike. Here are some of the key benefits:
- Enhanced Quality: The controlled injection process reduces the risk of defects and ensures a smooth surface finish, making it ideal for products that require precision.
- Complex Shapes: Low pressure casting excels at producing intricate shapes that would be challenging to achieve with other methods, giving designers greater flexibility.
- Material Efficiency: This process minimizes waste and allows for better utilization of material, leading to cost savings in production.
- Faster Production Times: With its rapid filling capability, the low pressure casting process significantly reduces cycle times, increasing throughput and efficiency.
- Versatility: It can accommodate a variety of metals and alloys, making it suitable for multiple industries, including automotive, aerospace, and consumer goods.
Applications of Low Pressure Casting
The versatility of the low pressure casting process allows it to be utilized across a wide range of applications. Here are some prominent industries leveraging this technology:
1. Automotive Industry
The automotive industry is one of the largest consumers of low pressure casting. Components such as engine blocks, transmission housings, and structural parts benefit from the process's ability to deliver lightweight yet durable pieces.
2. Aerospace Sector
In aerospace manufacturing, where precision and weight reduction are critical, low pressure casting produces components like turbine housings and structural elements. The high-quality surface finish is particularly beneficial for parts that undergo stringent inspection processes.
3. Consumer Electronics
Consumer electronics manufacturers leverage low pressure casting to create sleek and stylish product casings. The process allows for thin walls and intricate designs, essential for modern gadget aesthetics.
4. Art Supplies and Product Design
In the art supplies sector, the low pressure casting process enables designers to produce unique molds for sculptures and decorative items. Additionally, product design professionals can create prototypes and functional parts efficiently, thus accelerating the design cycle.
Advantages Over Other Casting Methods
The low pressure casting process stands out when compared to other casting techniques, such as gravity casting and high pressure die casting. Here are some key comparisons:
1. Defect Rate
Low pressure casting has a significantly lower defect rate due to the controlled filling process, resulting in fewer voids and imperfections in the final product.
2. Cost Efficiency
While high pressure die casting might offer high-speed production, the initial investment and operational costs can be high. Low pressure casting, conversely, balances speed and low operational costs, making it an appealing alternative.
3. Material Options
Many other casting techniques are limited to specific materials, while low pressure casting can work with a range of metals, expanding its usability in various sectors.
Challenges and Considerations
While the low pressure casting process has numerous benefits, it is essential to consider some challenges:
- Mold Design Complexity: Designing high-quality molds can be resource-intensive and requires meticulous planning.
- Material Costs: Depending on the metals used, material costs can fluctuate, thus impacting overall project budgets.
- Operational Expertise: Successfully executing low pressure casting requires skilled operators familiar with the nuances of the process.
Future Trends in Low Pressure Casting
The landscape of manufacturing is continuously evolving, and the low pressure casting process is no exception. Here are a few trends that might shape its future:
1. Automation and Robotics
As industries push towards automation, integrating robotics into the low pressure casting process is expected to enhance efficiency, precision, and safety.
2. Advanced Materials
Future advancements could see the use of next-generation materials, enabling even more sophisticated applications while maintaining optimal performance.
3. Sustainability Initiatives
Environmental concerns are leading manufacturers to adopt sustainable practices. The low pressure casting process, with its reduced waste production, is well-positioned in this initiative.
Conclusion
The low pressure casting process offers a revolutionary approach to manufacturing that balances quality, speed, and complexity. As businesses like arti90.com continue to explore the benefits of this technique, industries can expect to see enhanced product designs and increased operational efficiencies. By staying informed about the latest trends and advancements in low pressure casting, manufacturers can position themselves for success in an ever-evolving market.
In summary, whether you are an artist, a product designer, or a manufacturer, understanding the intricacies of the low pressure casting process is crucial for optimizing your production methods and keeping ahead of the competition.