Understanding Plastic Molding Manufacturers: A Comprehensive Guide
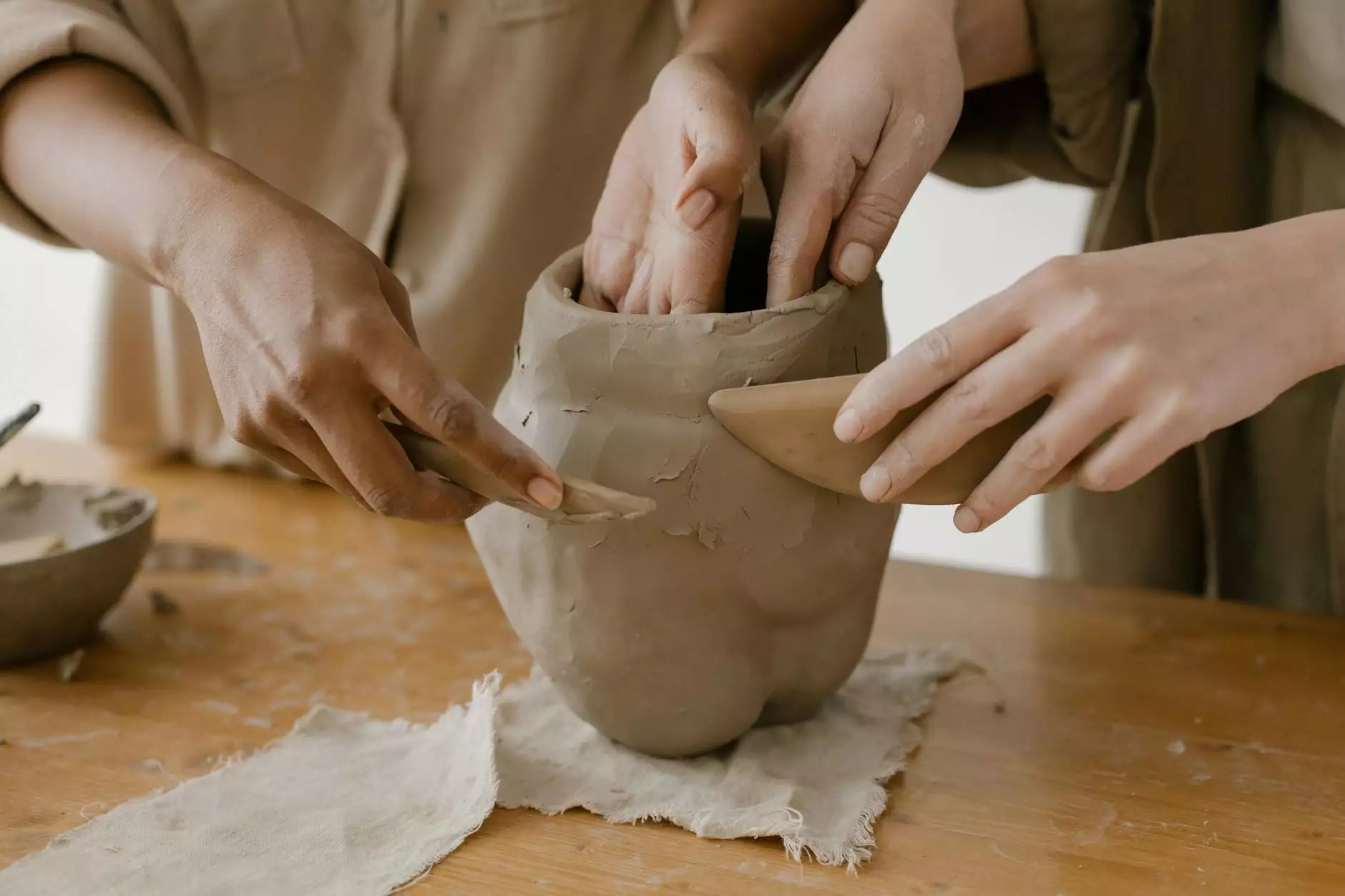
In the dynamic landscape of manufacturing, plastic molding manufacturers play a pivotal role, providing essential services that cater to various industries. From automotive components to consumer goods, the ability to mold plastic into functional forms has revolutionized production methods. This article delves deep into the intricacies of plastic molding, the processes involved, and why businesses increasingly rely on these manufacturers for their production needs.
What is Plastic Molding?
Plastic molding is a manufacturing process used to create parts by injecting molten plastic into a mold. The process involves several critical steps that ensure precision and efficiency. Here’s an overview of the main stages involved:
- Material Selection: The first step involves choosing the appropriate type of plastic resin based on the product’s required specifications.
- Heating: The selected plastic is heated until it reaches a molten state, allowing for easy flow into the molds.
- Injection: The molten plastic is injected into a pre-designed mold at high pressure.
- Cooling: After injection, the plastic is allowed to cool and solidify into the desired shape.
- Demolding: Finally, the hardened plastic part is removed from the mold, completing the manufacturing process.
This method, known as injection molding, is one of the most efficient and versatile techniques available within the industry.
The Importance of Plastic Molding Manufacturers
Plastic molding manufacturers are crucial in the supply chain as they provide the necessary expertise and resources to produce high-quality plastic components. Their importance can be highlighted through several key aspects:
- Cost Efficiency: By producing parts in bulk, these manufacturers significantly reduce the cost per unit, making it an economical choice for businesses.
- Precision and Consistency: Advanced machinery and experienced staff ensure that every part produced meets stringent quality standards, aiding in assembly and functionality.
- Diverse Applications: From automotive parts to medical devices, the adaptability of plastic molding can meet a wide range of industrial needs.
- Rapid Prototyping: Manufacturers can quickly create prototypes, allowing businesses to test and refine designs before committing to mass production.
- Sustainable Practices: Many plastic molding manufacturers are adopting eco-friendly techniques, including the use of recycled plastics and energy-efficient systems.
Types of Plastic Molding Processes
Within the realm of plastic molding, several distinct processes cater to different needs and product requirements. Understanding these can help businesses choose the right technique for their manufacturing demands:
1. Injection Molding
As mentioned earlier, injection molding is the most prevalent method of plastic molding. It is characterized by:
- High-volume production capabilities.
- Precision in intricate designs.
- A variety of materials that can be used, including thermoplastics and thermosets.
2. Blow Molding
Blow molding is typically used for producing hollow plastic objects, such as bottles. The process includes:
- Creating a parison (a tube-like piece of plastic).
- Inflating it into a mold to form the desired shape.
3. Rotational Molding
This technique is ideal for manufacturing large, hollow parts. The process involves:
- Heating plastic in a mold, which is rotated on two axes.
- Allowing the molten plastic to coat the interior of the mold evenly.
4. Thermoforming
Thermoforming involves heating plastic sheets to a pliable state and then forming them over a mold. Key points include:
- Commonly used for packaging and trays.
- Cost-effective for small production runs.
Choosing the Right Plastic Molding Manufacturer
When seeking a plastic molding manufacturer, it is important to consider various factors to ensure a successful partnership. Here are some tips:
- Experience and Reputation: Look for manufacturers with a proven track record in the industry.
- Capabilities: Ensure they have the necessary technology and expertise to handle your specific requirements.
- Quality Control Processes: Inspect their quality assurance protocols to guarantee high standards.
- Communication: Choose a manufacturer that communicates effectively and can provide regular updates throughout the process.
- Cost-Effectiveness: Compare quotes while considering the value of services offered rather than just the price.
The Future of Plastic Molding Manufacturing
The plastic molding manufacturing industry is poised for significant advancements in the coming years. Here are some trends to watch out for:
1. Advanced Manufacturing Technologies
With rapid technological advancements, manufacturers are incorporating automation and robotics into their processes, which enhances efficiency and consistency.
2. Sustainability Efforts
As environmental concerns rise, many plastic molding manufacturers are focusing on sustainability, adopting practices such as using biodegradable materials and reducing waste.
3. Customization and Flexibility
The demand for customized products is increasing. Manufacturers are investing in technologies that allow for greater flexibility in production runs.
Conclusion
Plastic molding manufacturers are integral to modern manufacturing, providing critical services that enhance production efficiency and product quality. By understanding the processes, benefits, and future trends, businesses can make informed decisions that not only cater to their current needs but also position them for growth in an evolving market.
As the industry continues to innovate, partnering with a reliable plastic molding manufacturer is essential for success. By focusing on quality, sustainability, and customer satisfaction, these manufacturers will serve as foundational pillars in the manufacturing ecosystem for years to come.