Transforming Ideas into Reality: The Role of a Rapid Prototype Company
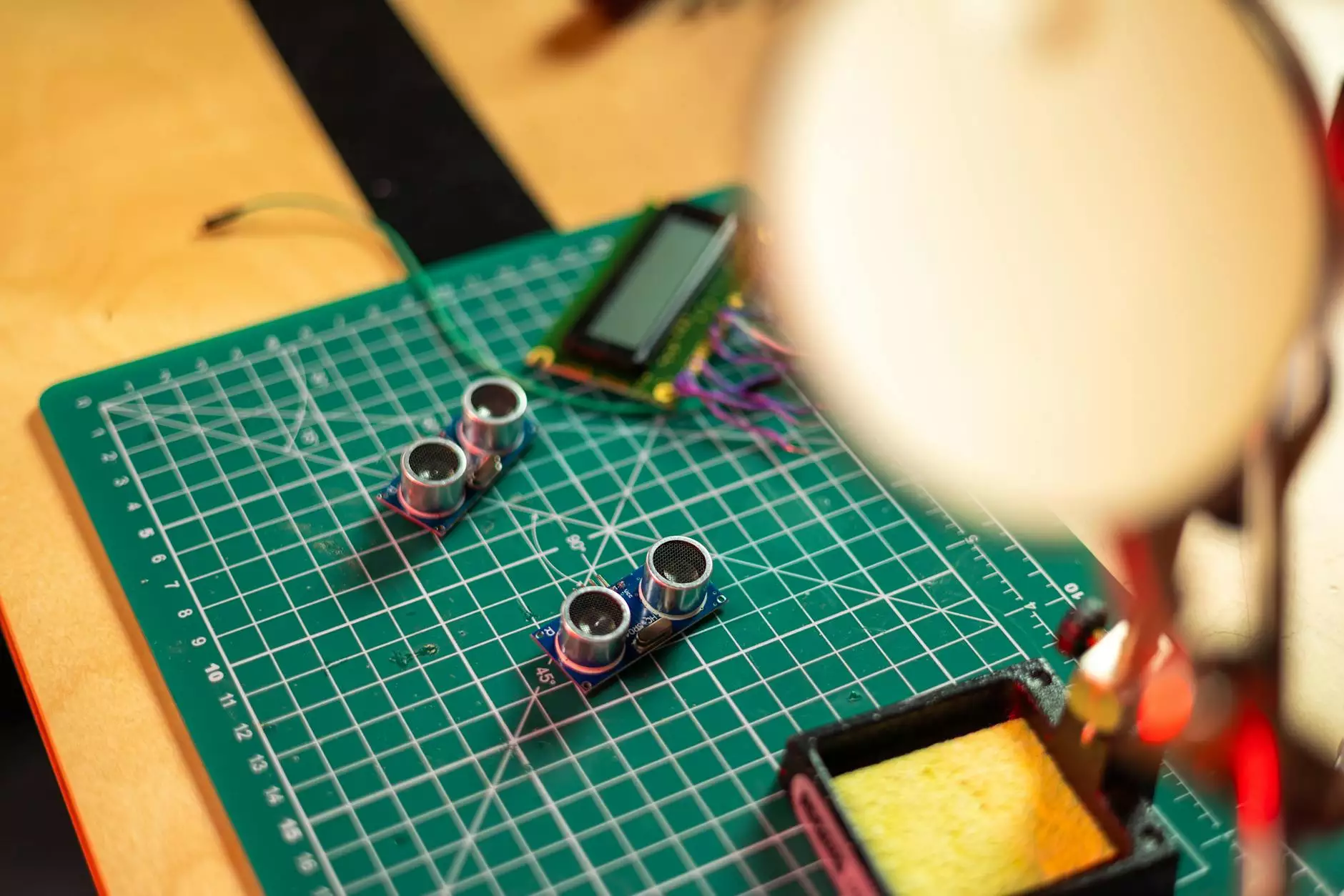
In today's fast-paced world, businesses are under constant pressure to innovate and deliver high-quality products that meet the evolving demands of consumers. This is where a rapid prototype company plays a crucial role. By providing rapid prototyping services, these companies enable businesses to quickly transform their ideas into tangible products. In this comprehensive article, we will explore the various aspects of rapid prototyping, its benefits, processes, and how companies like DeepMould.net can support your business in achieving its goals.
What is Rapid Prototyping?
Rapid prototyping is a process that allows designers and manufacturers to create a scale model of a product quickly and cost-effectively. This process utilizes various technologies, including 3D printing, CNC machining, and injection molding, to produce prototypes that can be tested and evaluated before full-scale production.
The primary purpose of rapid prototyping is to bridge the gap between concept and production. By creating prototypes, businesses can:
- Evaluate design concepts
- Test functionalities
- Identify design flaws
- Gather feedback from stakeholders
- Accelerate the product development cycle
The Importance of a Rapid Prototype Company
For companies in the manufacturing sector, partnering with a capable rapid prototype company like DeepMould.net can lead to several advantages:
1. Cost Efficiency
Developing a new product can be expensive, especially when it involves traditional methods of production. Traditional prototyping methods often require significant investments in molds and tooling, which can lead to high initial costs. With rapid prototyping, businesses can produce prototypes without the need for extensive tooling, thereby reducing costs significantly.
2. Time Savings
In a competitive market, time is of the essence. Rapid prototyping allows businesses to reduce the time taken from the concept phase to the production phase. Prototypes can be developed in days or weeks instead of months, enabling companies to launch products faster and gain a competitive edge.
3. Improved Collaboration and Communication
Having a physical prototype makes it easier for teams to collaborate and communicate. Designers, engineers, and stakeholders can evaluate the prototype, provide feedback, and make necessary adjustments in real time. This collaborative approach ensures that the final product meets the expectations and requirements of all involved parties.
4. Enhanced Product Quality
Testing prototypes early in the design process helps identify issues before production begins. A rapid prototype company can help conduct necessary tests, ensuring that flaws are addressed in the design phase. This results in a higher quality final product that satisfies customer needs.
Technologies Used in Rapid Prototyping
Rapid prototyping encompasses a variety of technologies, each suited to different applications.
1. 3D Printing
3D printing, or additive manufacturing, is one of the most commonly used methods in rapid prototyping. It builds parts layer by layer, allowing for intricate designs that would be difficult to achieve with traditional methods. Companies use various materials in 3D printing, including plastic, metal, and even biocompatible materials for medical applications.
2. CNC Machining
Computer Numerical Control (CNC) machining is another prevalent method in rapid prototyping. It involves using computerized controls to operate machine tools, producing highly precise and intricate components. CNC machining is ideal for creating metal parts and is widely used in industries such as aerospace and automotive.
3. Injection Molding
Although traditionally associated with mass production, injection molding can also be used for producing high-quality prototypes. This method involves creating molds that can replicate the final product's design. While injection molding requires higher upfront costs for molds, it offers significant benefits in terms of accuracy and surface finish.
The Rapid Prototyping Process
The process of rapid prototyping generally involves several key steps:
- Concept Development: Initiate the prototyping process by defining the concept and requirements of the product.
- Design Creation: Using CAD software, design the prototype while considering manufacturing constraints and materials.
- Prototype Production: Choose a suitable prototyping technique (e.g., 3D printing, CNC machining) and produce the first prototype.
- Testing and Evaluation: Test the prototype to gauge its performance and gather feedback from team members.
- Refinement: Based on feedback, make necessary modifications to the design and produce a revised prototype.
- Final Production: Once the prototype meets the desired criteria, prepare for full-scale production.
Case Studies: Real-World Applications of Rapid Prototyping
Case Study 1: Automotive Industry
The automotive sector is one of the most significant beneficiaries of rapid prototyping. Consider a company that develops new vehicle models. By utilizing a rapid prototype company, they can create functional components like dashboard interfaces, engine parts, or even entire body panels swiftly. This process allows them to test aerodynamics, functionality, and ergonomics extensively before moving on to mass production.
Case Study 2: Medical Devices
In the medical field, prototypes need to meet stringent regulatory standards. A medical device company that collaborates with a rapid prototype company can quickly develop and test surgical instruments or diagnostic equipment. Rapid prototyping enables healthcare innovators to iterate designs based on real-world feedback effectively. The ability to create high-quality and compliant prototypes allows them to accelerate the time to market.
Challenges in Rapid Prototyping
Despite the numerous advantages, there are challenges associated with rapid prototyping:
1. Material Limitations
While many materials are available for rapid prototyping, not all are suitable for every application. Understanding the limitations of each material and its suitability for the final product is crucial for success.
2. Cost Considerations
The initial costs of some rapid prototyping methods (especially when using advanced technologies like CNC machining or high-quality 3D printers) can be high. Companies must balance these costs against the benefits of faster production and reduced time to market.
3. Skills and Expertise
Successful rapid prototyping requires expertise in various technologies and understanding of design principles. A lack of in-house skills may hinder the effectiveness of the process.
Choosing the Right Rapid Prototype Company
When selecting a rapid prototype company, consider the following factors:
- Experience: Look for a company with a proven track record in your industry.
- Technology Capabilities: Ensure they utilize the latest technologies that suit your project needs.
- Material Options: Assess the range of materials they can work with.
- Customer Support: Choose a provider that offers excellent customer service and support throughout the prototyping process.
- Turnaround Time: Evaluate their ability to deliver prototypes quickly without compromising quality.
Conclusion
In conclusion, a rapid prototype company like DeepMould.net plays an essential role in the modern manufacturing ecosystem. By leveraging advanced technologies and processes, these companies help businesses bring their ideas to life efficiently and effectively. The ability to create prototypes rapidly not only accelerates time to market but also enables companies to innovate, improve product quality, and ultimately delight customers. For manufacturers, investing in a partnership with a reliable rapid prototyping service can make all the difference in navigating the challenges of today’s competitive landscape. Embrace the future of product development by considering rapid prototyping as a vital part of your innovation strategy.